Construction ERP
How ERP is Revolutionizing Modular Construction
Last updated:
July 7, 2025
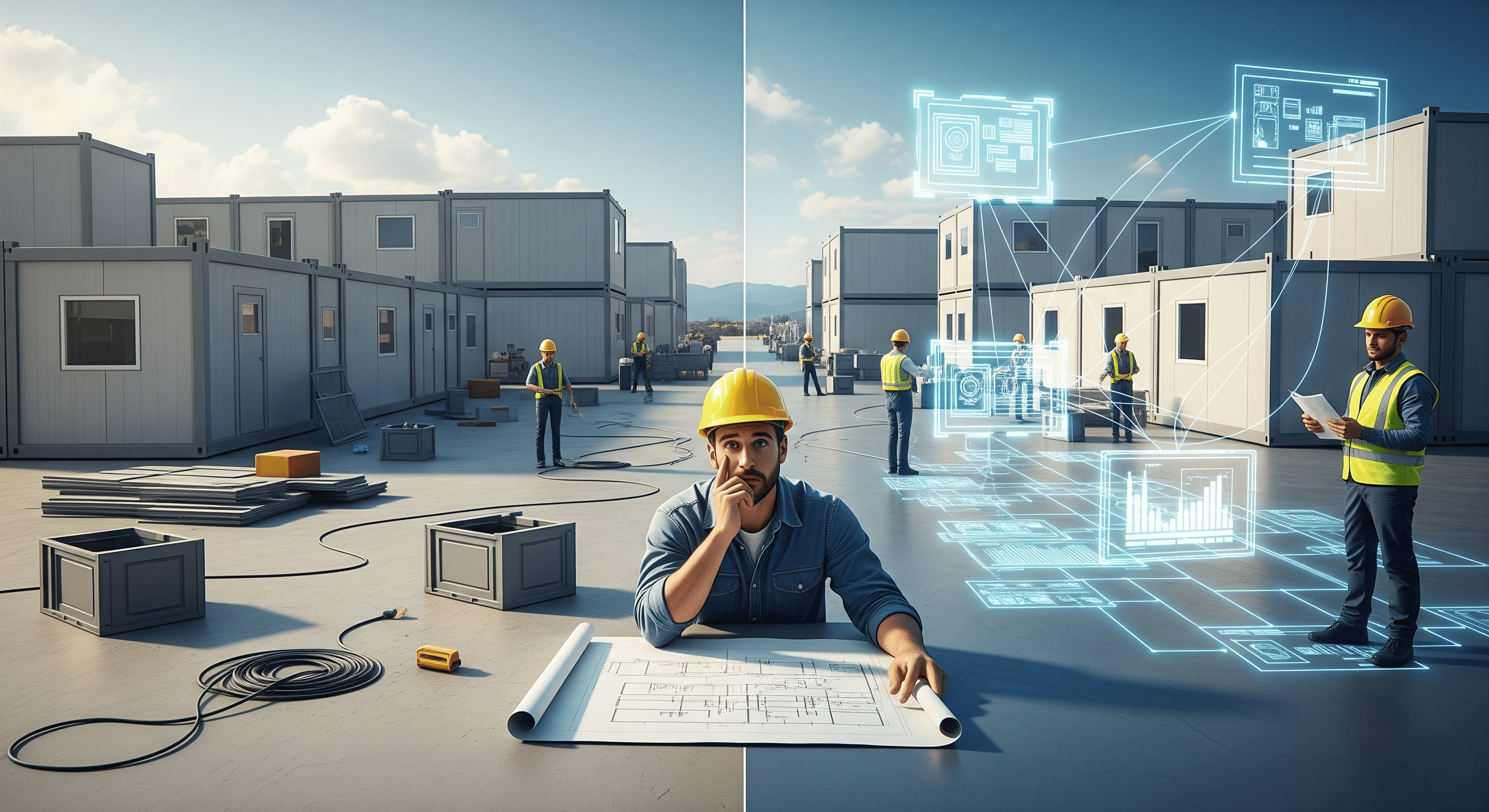
Why Is Modular Construction Still Struggling With Efficiency?
Envision this — you've got a big modular build project in the pipeline.
Everything's great — your designs are complete, the factory production started, and the site is ready for assembly. But lo and behold, materials don't materialize when they should, factory crews sit idle, and on-site assembly lags.
The outcome? Deadlines miss the mark, costs escalate, and clients are infuriated.
This is where most modular construction projects fail. While it holds out the promise of being faster, cost-effective, and minimizing waste, modular construction still has operational bottlenecks that bring the whole process to a crawl.
And the reason why? Insufficient centralized control and poor coordination among stakeholders.
But here's the good news: ERP (Enterprise Resource Planning) is changing the way modular construction gets done by eliminating inefficiencies and streamlining resource management end-to-end.
In this blog, we’ll break down:
- The top challenges modular construction faces.
- How ERP solves those challenges effortlessly.
- What features to look for when choosing an ERP.
Let’s get into it.
4 Major Challenges in Modular Construction
Even though modular construction is faster and more cost-effective, it still faces operational chaos that traditional construction projects often bypass.
Here’s where most modular projects hit roadblocks:
1. Complex Supply Chain Management
The Problem:
In modular construction, materials, modules, and equipment are procured from various vendors, usually located across regions or even nations. Monitoring the arrival of every shipment, making sure it arrives on time, and keeping inventory tabs becomes a logistical nightmare.
What Goes Wrong:
- Material delays stop factory production dead in its tracks.
- Incorrect inventory monitoring creates unplanned shortages.
- Inefficient supplier communication kills the workflow.
The outcome? Your project timeline goes down like a house of cards.
2. Communication Gaps Among Stakeholders
Modular construction requires multiple parties:
- Designers draw up the plan.
- Factories produce the modules.
- Suppliers deliver the materials.
- Field teams assemble on site.
Now consider this — your designer makes a last-minute alteration, but the factory isn't notified in time. Or your supplier changes delivery, but the site manager is unaware. That's how miscommunication creates expensive mistakes.
Without live communication, the whole chain collapses.
3. Budgeting & Scheduling Inefficiencies
Budget overruns are the worst nightmare of modular construction. Why? Because even a small delay in material supply or misappropriation of resources can lead to:
- Higher labor costs.
- Delays in completion.
- More rework expenses.
And since modular construction depends much on factory production schedules, any disruption has a ripple effect, impacting the whole project budget and timeline.
4. Increased Costs & Production Delays
Time is money in modular construction. If a single component does not arrive on schedule, the whole assembly grinds to a halt — with:
- Production downtime.
- Labor hours wasted.
- Delayed project completion schedules.
The greatest reason? Lack of centralized control to track material flow, labor productivity, and production output. This is where ERP comes in and turns things around.
How ERP Transforms Modular Construction
Here's where things shift. Rolling out ERP (Enterprise Resource Planning) can transform your modular construction mess into a finely tuned machine.
An ERP system is the control center — linking all parties involved, tracking resources, streamlining workflows, and offering real-time visibility into project status.
Here's how ERP revolutionizes modular construction:
1. Real-Time Data for Better Decision-Making
Picture having access to track:
- Material inventory levels.
- Module production progress.
- Labor productivity.
- Delivery schedules.
… all in real-time through a single dashboard.
ERP software offers real-time insight into every aspect of project operations, enabling project managers to make quicker, fact-based decisions. Guesswork disappears, as does the wasteful delay it causes.
2. Automated Resource & Inventory Management
Materials go from suppliers → factories → sites in modular construction. Without ERP, manually following their movement is a logistical nightmare.
ERP automates:
- Material purchasing based on forecasted demand.
- Real-time inventory tracking.
- Resource allocation according to production capacity.
The outcome?
- No more surprises with material shortage.
- No more production stoppage.
- Smooth supply chain management.
3. Predictive Analytics for Risk Management
This is where ERP becomes the future. AI-driven predictive analytics enables ERP to:
- Predictive delays.
- Discover cost overruns.
- Forecast material shortages.
With this, project managers can rectify issues even before they crop up — in terms of saved time, curbed costs, and on-budget projects.
4. Smooth Interaction Between Office & Field Teams
One of the most significant ERP game-changers is the way it links office teams (procurement, finance, designers) with field teams (factory production, site assembly).
No more waiting for manual updates with ERP:
- Live project status.
- Real-time design updates.
- Instant material availability notifications.
This prevents miscommunication, and the entire project just runs like clockwork.
What to Look for in a Construction ERP
The key to modular construction success is selecting the correct ERP system. Here's what you need to place top priority on:
1. Access in the Cloud
A cloud-based ERP gives all stakeholders remote access to project information at all times. This guarantees:
- Increased approvals.
- Timely project visibility.
- Rapid resolution of logjams.
2. Personalization & Versatility
No two modular construction projects are identical. Select an ERP that has:
- Customizable workflows.
- Variable reporting dashboards.
- Personalized notifications/alerts.
This will ensure your ERP is tailored to your specific project needs.
3. AI and Machine Learning Functionalities
An updated ERP with Machine Learning (ML) and Artificial Intelligence (AI) assists you in:
- Predicting shortages in materials.
- Preempting cost overruns in budgets.
- Enhancing labor productivity.
This helps you anticipate the disruptions before they happen.
4. Integration with Current Tools
- Your ERP needs to integrate without a hitch with:
- Design applications (CAD, BIM).
- Supplier management programs.
- Accounting systems.
This builds a seamless ecosystem in which all departments coexist.
The Future of ERP in Modular Construction
The future revolution in modular construction will be fueled by intelligent ERP systems coupled with:
1. IoT (Internet of Things)
Think of receiving real-time information from:
- Material delivery trucks.
- Factory equipment.
- Assembly progress on-site.
ERP coupled with IoT will give 100% real-time visibility, no guesswork.
2. AI-Powered Forecasting
The future ERP systems will employ AI to:
- Forecast delivery delays.
- Optimize labor scheduling.
- Predict production costs.
This guarantees zero downtime and maximum productivity.
3. Robotics & ERP Integration
In the future, ERP will control directly:
- Robot arms building modules.
- Automated stock movement.
- Resource allocation on site.
This will reduce human errors, shorten production time, and lower operational expenses.
Conclusion: Why Modular Construction Should Adopt ERP Now
The largest reason why modular construction projects are plagued with delays, cost overruns, and communication failures is lack of centralized control. ERP addresses this by:
- Simplifying resource management.
- Giving real-time visibility.
- Closing communication gaps.
In a world of speed and cost-effectiveness dominating modular construction, ERP investment is no longer an indulgence — it's essential.
Ready to revolutionize your modular construction efficiency? Begin by discovering how ERP can transform your entire operation.